Выбросы смесильно-прессовых отделений включают пековые газы и газы смолистых веществ, состоящие из полициклических ароматических углеводородов (ПАУ). Выбросы приводят к созданию неприятных запахов и до определенной степени являются канцерогенными. Современные методики очистки отходящих газов сухим поглощением недостаточны для борьбы с загрязнением атмосферы летучими пековыми газами и газами смолистых. В настоящее время технология регенерационного термического окисления (РТО) обеспечивает разрушение конденсированных и летучих ПАУ. Два года безотказной эксплуатации на печи обжига анодов продемонстрировали возможность снижения вредных выбросов, как минимум, на порядок. Новая конструкция, обеспечивающая очистку выбросов печи обжига и смесильно-прессового отделения одной установкой РТО, существенно упрощает очистку отходящих газов смесильно-прессового отделения. Данный подход раз и навсегда решает проблемы выбросов смесильно-прессового отделения.
1. ВЕРОЯТНОСТЬ КОНФЛИКТОВ, СВЯЗАННЫХ С ВЫБРОСАМИ СМЕСИЛЬНО-ПРЕССОВЫХ ОТДЕЛЕНИЙ
Существует достаточное количество веских оснований для размещения промышленных зон по соседству с жилыми районами. Наличие жилых районов, инженерных коммуникаций, субподрядчиков по поставкам и транспортных систем - лишь некоторые из доводов для строительства заводов в заселенных районах. Для предупреждения конфликтов, связанных с промышленными выбросами санитарно-защитные зоны обычно располагают между городскими районами и промышленными комплексами. В действительности, требования о создании санитарно-защитной зоны являются неоспоримыми. Само собой разумеется, через некоторое время жители начнут жаловаться на промышленные выбросы. В настоящей статье рассматриваются выбросы смесильно-прессовых отделений. Общие выбросы алюминиевых заводов состоят из атмосферных выбросов цеха анодной массы и печи обжига анодов и включают видимые полициклические ароматические углеводороды (ПАУ) с неприятным запахом и являющиеся канцерогенными. Как следствие, выбросы смесильно-прессовых отделений приводят к высокой вероятности конфликтов с населением, живущим в непосредственной близости от завода.
2. СОВРЕМЕННЫЙ КОНТРОЛЬ ПРОМЫШЛЕННЫХ ВЫБРОСОВ
На Рис. 1 показано смесильно-прессовое отделение и его основные компоненты. На Рис. 2 представлена технологическая блок-схема смесильно-прессового отделения.
Кроме "критических выбросов" - жидких и твердых отходов - смесильно-прессовое отделение отвечает за выбросы цеха анодной массы и огнеупорные кирпичи. Данный вопрос рассматривается в документе ‘WASTE MATERIALS IN ANODE MANUFACTURING; AN OVERVIEW [1]. (ОТХОДЫ ПРИ ПРОИЗВОДСТВЕ АНОДОВ. ОБЗОР [1]). Выбросы двуокиси серы в смесильно-прессовых отделениях ничтожно малы по сравнению с выбросами SO2 алюминиевого завода.
В настоящее время проектная мощность алюминиевых заводов составляет до одного миллиона тонн алюминия. Для таких заводов необходимы смесильно-прессовые отделения производительностью 500000 тонн в год и более. Абсолютная величина (канцерогенных) выбросов таких отделений составляет порядка 200000 кг в год. Большую часть компонентов смолистых и пека в отходящих газах отделения представляют летучие вещества (т.е. не конденсированные). С этими летучими выбросами установки сухой абсорбции не справляются. Таким образом, сухая абсорбция не эффективна, не может предотвратить конфликты с соседствующим населением и не отвечает нормальным стандартам охраны труда. Необходим абсолютно новый подход.
3. НОВЫЙ ПОДХОД К СНИЖЕНИЮ ВЫБРОСОВ СМЕСИЛЬНО-ПРЕССОВЫХ ОТЕДЕЛЕНИЙ
От "типовой" ситуации оптимизированное по выбросам смесильно-прессовое отделение отличается следующим:
- Разгрузка нефтяного кокса не краном, а выгрузным пневмотранспортером.
- Последнее поколение рукавных фильтров, оборудованных высококачественными рукавами, гарантирующими концентрации выбросов пыли до 10 мг/Нм3 пыли твердых частиц 10, т.е. мелкой пыли с частицами размерами от 0 до 10 μм и практически без более крупной пыли.
- Снижение выбросов газообразного пека и смолистых в смесильно-прессовое отделении, заготовке анодов, печи обжига анодов за счет установки регенерационного термического окисления вместо установок сухой абсорбции.
3.1 Потенциально возможные результаты снижения выбросов пыли
В течение многих лет для "стандартных рукавных фильтров" приемлемым уровнем концентрации пыли считалась 50 мг/Нм3 (твердые частицы пыли 10). Соответствующая конструкция рукавных фильтров последнего поколения обеспечивает выбросы с концентрацией пыли ≤10 мг/Нм3 по твердым частицам 10. При замене системы разгрузки краном в бункер выгрузным пневмотранспортером неконтролируемые выбросы пыли в атмосферу сокращаются практически до нуля. Разгрузка краном в бункер приводит к выбросам крупных частиц пыли. Несмотря на то, что крупные частицы пыли не являются вредными для здоровья, они приводят к снижению видимости. Данная проблема решается выгрузным пневмотранспортером. Рукавные фильтры последнего поколения и выгрузной пневмотранспортер являются "хорошо зарекомендовавшими себя технологиями" и не заключает в себе неоправданных рисков при использовании данных методов снижения выбросов. Выгрузка нефтяного кокса пневмотранспортером подвергалась сомнению из-за возможного риска разрушения зерен. Доказано, что дробление на фрагменты носит ограниченный характер и относится только к тем зернам, дробление которых неизбежно при подготовке сухой шихты. При использовании описанных методов снижения выбросов выбросы пыли снижаются в 10 раз. Поэтому, проблему выбросов пыли можно считать решенной.
3.2 Снижение выбросов ПАУ с помощью установки регенерационного термического окисления (РТО)
Еще в начале восьмидесятых годов 20го столетия специалисты осознавали перспективность сжигания пековых газов и газов смолистых веществ [2]. Вместе с тем, в то время решение всех технических проблем, связанных с рекуперацией энергии, не представлялось возможным просто из-за отсутствия соответствующей технологии. Считалось, что без рекуперации энергия, необходимая на сжигание пековых газов и газов смолистых веществ, в два-три раза превысит количество энергии, необходимой для производства анодов. При столь большой потребности в энергии сжигание в качестве метода снижения выбросов не представлялось возможным.
С тех пор в материаловедении были достигнуты значительные успехи. Тем не менее, использование технологии дожигания в рекуперации энергии представляло собой определенные трудности. В типовом смесильно-прессовом отделении на печь обжига приходится от 80% до 90% всех смолистых, состоящих из конденсированных и летучих компонентов. Остальные выбросы смолистых приходятся на хранилище жидкого пека, цех анодной массы и заготовку анодов.
Первый успешный опыт системы регенерационного сжигания был применен в очистке отходящих газов цеха анодной массы и заготовки анодов [3, 4]. Первые попытки очистки отходящих газов печи обжига успеха не имели из-за технологических сложностей. Эти проблемы были успешно решены. На момент написания настоящей статьи в течение двух лет на принципе "Регенерационного термического окисления (РТО) [5, 6]" успешно и безостановочно работает установка "Autotern", очищающая отходящие газы кольцевой печи обжига с открытым верхом производительностью 100000 тонн в год с хорошо зарекомендовавшей себя системой управления технологическим процессом печи обжига, поставляемой R&D Carbon Ltd.
3.3 Технология регенерационного термического окисления
Сжигание пековых газов и газов смолистых – единственный возможный подход к удалению вредных выбросов. Сжигание этих компонентов осуществляется напрямую. Проблемы заключаются в том, что количество отходящих газов существенно, а температура газа низкая, теплотворная способность примесей ничтожно мала. Для сжигания необходима температура около 800°C. Как следствие, затраты энергии при простом процесс сжигания составляют недопустимую величину.
При использовании технологии регенерационного термического окисления энергия горячих газов используется после сжигания примесей для нагрева теплообменника. Камера сгорания прямо связана с двумя камерами теплообмена, заполненными пакетами керамических элементов, как показано на Рис. 3 и 4.
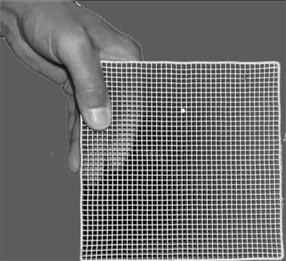
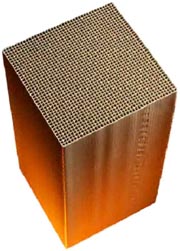
Пакет одинаковых элементов приводит к созданию ламинарного потока с низким аэродинамическим сопротивлением. Большая площадь поверхности обеспечивает высокую эффективность теплопередачи. Как указывалось выше и как показано на Рис. 5, камера сгорания прямо соединена с двумя одинаковыми теплообменниками. Направление газового потока в камере сгорания меняется на обратное через короткие промежутки времени – обычно через две минуты, как показано стрелками 1 и 2.
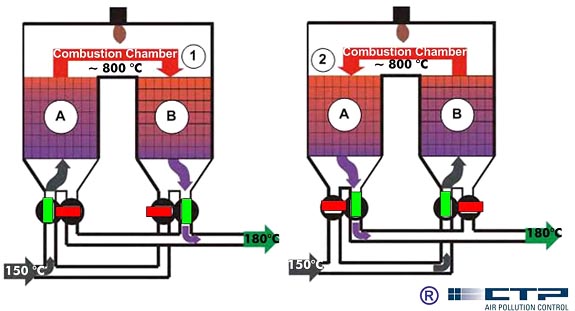
Слева на рисунке показан поток необработанного газа из печи, проходящий через теплообменник "А". Холодный газ нагревается горячими керамическими элементами. После сгорания примесей очищенный газ поступает в теплообменник "В" (стрелка 1) и нагревает теплообменник "В". После этого очищенный и охлажденный газ подается в установку абсорбции фтористого водорода (не показана). Как правило, через две минуты клапаны под теплообменником действую таким образом, что неочищенный газ теперь поступает на теплообменник "В" (на рисунке 5 - справа). После этого газ проходит через камеру сгорания, как показано стрелкой 2, и нагревает теплообменник "А". Через две минуты вновь запускается такой же цикл. Для обеспечения соответствующей производительности и резервирования мощности параллельно можно вести работу трех или четырех таких установок.
Удаление фтористого водорода производится на известняке в установке сухой абсорбции после РТО. Из этой установки газ выделяется в атмосферу через трубу.
В случае высокой нагрузки конденсированных смолистых может возникнуть необходимость в фильтрационной установке предварительной очистки, улавливающей капли смолистых на керамических элементах. Установка предварительной очистки очищается прожиганием фильтров через регулярные промежутки времени.
3.4 Использование РТО при очистке отходящих газов цеха анодной массы и заготовки анодов
В цехе анодной массы температура отходящих газов ниже, чем в печи обжига анодов, что приводит к конденсированию пековых газов в трубопроводах. Попытка предварительного нагрева газов раздельными нагревателями показала неэффективность и сложность данного подхода. Новый запатентованный подход [7] устраняет необходимость раздельного нагрева отходящих газов. В соответствии с данных подходом горячие отходящие газы из установки РТО печи обжига анодов используются в качестве носителя "холодных" отходящих газов с производства зеленых анодов. Меньшее количество отходящих газов производства зеленых анодов по сравнению с количеством отходящих газов печи обжига позволяет смешивать отходящие газы производства зеленых анодов с отходящими газами печи обжига. При этом очистка всех отходящих газов с содержанием ПАУ производится в одной комбинированной установке РТО или на "Установке комбинированной газоочистки".
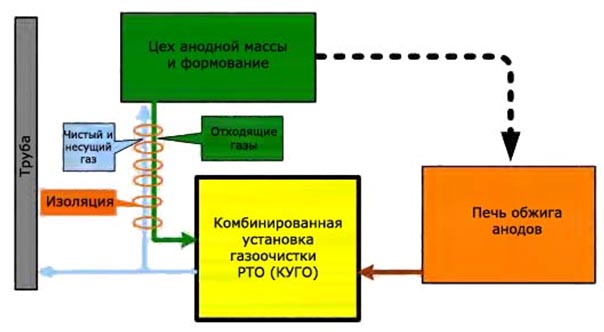
Количество газа и общее количество выбросов углеводородов (например, общее количество смолистых) смесильно-прессового отделения с годовой производительностью 500000 показано на рис. 7.
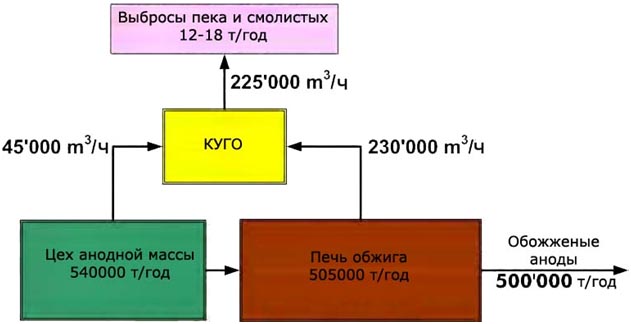
4. ПОГРАНИЧНЫЕ УСЛОВИЯ ЭКСПЛУАТАЦИИ ПРИ МИНИМАЛЬНЫХ ВЫБРОСАХ
Для снижения выбросов до минимума необходима соответствующая конструкция установки, ее правильное обслуживание и рациональная эксплуатация. Ниже приведены примеры условий, необходимых для эксплуатации с минимальными выбросами:
- Бездефектность и хорошее качество эксплуатируемых рукавных фильтров.
- Оборудование печи обжига анодов современной системой управления технологическим процессом для оптимального сжигания газов смолистых.
- Регулярный контроль за выбросами.
- Обучение эксплуатационного и обслуживающего персонала, направленное на обеспечение минимума выбросов.
5. ВЫВОДЫ: РТО - АБСОЛЮТНЫЙ ПОДХОД К СНИЖЕНИЮ ВЫБРОСОВ СМОЛИСТЫХ СМЕСИЛЬНО-ПРЕССОВОГО ОТДЕЛЕНИЯ
Газы смолистых и пековые газы, образующиеся при производстве зеленых анодов и при обжиге анодов, несомненно, представляют одну из самых острых проблем, связанных с выбросами при производстве анодов. Сухая адсорбция в том виде, в каком она существует в настоящее время, неспособна улавливать летучие компоненты и снижать выбросы смолистых и пека до приемлемых уровней. Как показано в Таблице 1 и на Рис. 8 замена сухой адсорбции на регенерационное термическое окисление (РТО) снижает выбросы в 10 и более раз при приемлемых затратах на снижение выбросов. При РТО подходе остающиеся выбросы составляют ничтожно малую величину. Таким образом, можно сделать вывод, что проблемы выбросов, связанных с производством анодов, в настоящее время решены.
Таблица 1: Сравнение выбросов типового и современного смесильно-прессового отделения производительностью 100000 т/год.
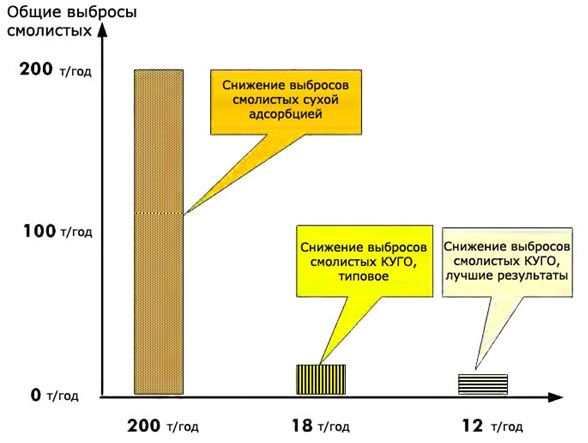
БЛАГОДАРНОСТИ
Авторы выражают благодарность компании “CTP Air Pollution Control” (Грац, Австрия) за предоставленную информацию об оборудовании РТО ‘Autotherm’ RTO и компании ALUCHEMIE (Роттердам) за информации об эксплуатации РТО.
ЛИТЕРАТУРА
1. KELLER F. (1994) ‘Waste Materials in Anode Manufacturing; an Overview’, Light Metals, TMS, San Francisco, p. 599 - 607.
2. VDI 3467 Emission Control. Production of carbon and artificial graphite (1982). Verein Deutscher Ingenieure. VDI-Handbuch Reinhaltung der Luft, Band 2.
3. Частное сообщение.
4. Biotox RTO for anode paste preparation, supplied by: Biothermica (www.biothermica.com).
5. KOOIJMAN A. et al. (2005) ‚Experience with Regenerative Thermal Oxidation as a Fume Treatment Technology for an Open Ring Type Anode Baking Furnace’, ed. Halvor Kwande, Light Metals, TMS, San Francisco.
6. Chemisch Technische Prozesstechnik GmbH (2005):“CTP Compact RTO 2 Bed/Multibed” Sales Brochures, Graz, Austria, supplied by CTP (www.CTP.at).
7. Swiss Patent 00604/05: Abgasreinigung in einer Fabrikanlage zur Herstellung von Formkörpern aus Kohlenstoff’.