Введение
Emirates Aluminium Company (EMAL) - совместное предприятие производителя алюминия Dubai Aluminium Company (DUBAL) и компании Mubadala Development Company (MUBADALA). Первая очередь алюминиевого завода EMAL, расположенного у нового порта Халифа в промышленной зоне Эмирата Абу Даби введена в действие 2 декабря 2010 года. С завершением первой очереди годовая производительность составит 750000 тонн алюминия - завод станет самым крупным проектом нового строительства в мире. В настоящее время на двух сериях силой тока 350 кА по технологии DX в эксплуатации находятся 756 электролизеров.
EMAL производит обожженные аноды для завода на двух печах обжига номинальной годовой производительностью 450000 тонн обожженных анодов. Работающие на газе печи обжига с открытым верхом, поставленные компанией Riedhammer, оборудованы системой огня R&D Carbon. Идентично спроектированные две печи обжига состоят из 64 камер, 9 огневых простенков и 8 кассет, как показано на Рис. 1 и 2.
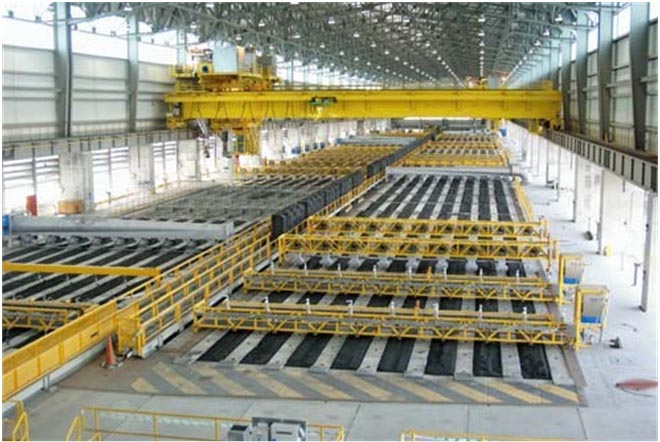
На каждой печи установлено 4 огня, каждый оборудован одним вытяжным манифольдом, одной рампой контроля разрешения, тремя горелочными мостиками и двумя воздушными охладителями.
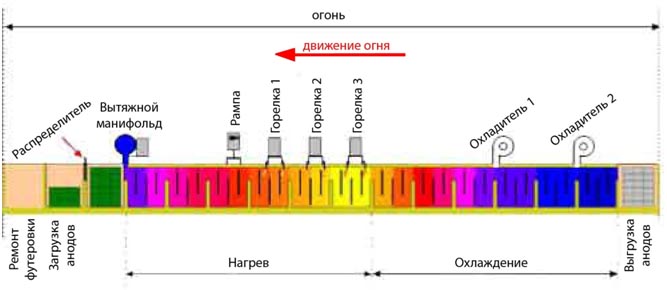
Кассеты рассчитаны на 4 слоя по 7 анодов в каждом весом зеленых и обожженных анодов, соответственно, 1155 и 1100 кг. Эксплуатация печи при цикле огня от 26.7 до 29 часов обеспечивает производительность кассеты 865 кг/час (т.е. 21 анод x 1100 кг/ 26.7 час). При типовом уровне производительности на кассету других печей, составляющем 759 кг/час, фактическая производительность печей EMAL намного выше.
Для поддержания удельной производительности кассеты на таком уровне, основу необходимо было подготовить на уровне проектирования обеих печей обжига и системы огня.
При проектировании кассет с повышенной удельной производительностью возникли, в частности, следующие проблемы:
- Однородность распределения температуры на всех этапах обжига для обеспечения однородности качества [1]
- Управление сгоранием пека, обеспечивающее полное сгорание всех летучих пека для снижения до минимума потребления энергии и выбросов [2]
- Управление процессом охлаждения для повышения эффективности охлаждения и уменьшения до минимума потребления материала пересыпки
Для решения этих задач на обеих печах и в системе огня внедрены многочисленные конструктивные особенности. Для решения тепловых и динамических аспектов использовалось термодинамическое моделирование (CFD) [3]. Основой для понимания связи между характеристиками анодного сырья, производственными параметрами и полученным в результате качеством анодов стал более чем 40-летний опыт опытно-конструкторских работ [4, 5, 6]. Эти знания позволили использовать гибкость системы огня для выбора материалов, наиболее подходящих для условий обжига с оптимальной кривой обжига, адаптированной к свойствам сырья и зеленых анодов.
В настоящей статье представлены задачи, возникшие во время проектирования и достигнутые результаты.
Распределение температуры и качество анодов
Принципиальное требование к обжигу анодов заключается в обеспечении одинаковой тепловой обработки с равномерным распределением тепла в каждый момент времени для всех анодов.
Для количественного определения распределения температуры в выбранных кассетах конкретной камеры было проведено измерение размера кристаллитов. В два внешних ниппельных гнезда всех анодов в разных камерах печи ABF 1, работающей с циклом огня 28, были вставлены графитовые тигли, заполненные зеленым коксом. После обжига графитовые тигли вынимались из выгруженных анодов, после чего проводилось измерение размеров кристаллитов обожженного (ранее зеленого) кокса. На основании калибровки, проведенной в течение 20 часов выдержки при максимальной температуре, выведено соотношение между размером кристаллитов Lc и истинной температурой.
На Рис. 4 показано распределение истинной температуры в топовой кассете на основании значений Lc. Рассмотрено 126 значений - во всех кассетах, на которых проводились измерения, распределение температуры (средняя T +/- 2σ = 1'102 +/- 27°C) было отличным и репрезентативным для всей печи обжига.
Несмотря на то, что измерения размеров кристаллитов проводились при нормальной работе печи, измерения остаются выборочными. Контроль над обеспечением качества анодов, проводимый в процессе производства, является обязательным для количественного определения развития в долговременной перспективе. Для оценки процесса обжига, свойства, находящиеся под воздействием окончательной температуры и скорости нагрева, можно рассматривать, исключая любые изменения в качестве материалов и эксплуатации цеха анодной массы:
- Истинная плотность
- Размер кристаллитов Lc
- Удельное электрическое сопротивление
- Теплопроводность
- Прочность на изгиб
- Реакционная способность в потоке СO2
- Реакционная способность в потоке воздуха
В качестве примера на Рис с 5 по 7 приведена эволюция некоторых свойств анодов. Красные линии указывает на верхний и/или нижний пределы.
Временное смещение удельного электрического сопротивления (см. Рис.5) вызвано колебаниями в сырьевых материалах. Соответствующие показатели истинной плотности свидетельствуют об очень равномерной окончательной температуре обжига.
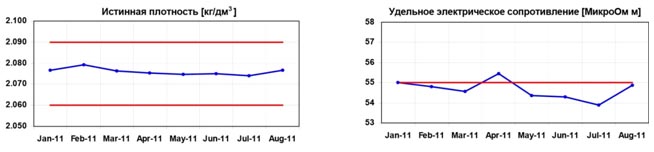
Колебания и, в частности, резкое увеличение остатка в опыте реактивности в токе воздуха в июле и августе 2011 года вызваны колебаниями содержания ванадия в нефтяном коксе. Постоянство высокого содержания остатка в опыте реактивности в токе CO2 свидетельствует об оптимальности процесса обжига.
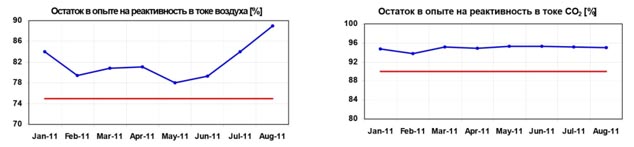
Высокий уровень прочности на изгиб свидетельствует о хорошей управляемости скоростью нагрева. Несмотря на то, что процесс обжига оказывает первостепенное влияние на воздушную проницаемость, этот показатель находится на очень низком уровне и служит еще одним подтверждением отличного качества анода.
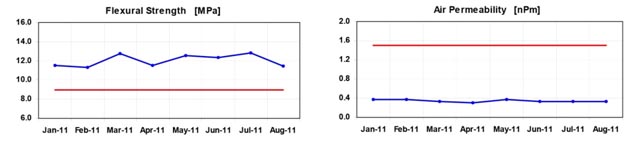
Из рисунков с 5 по 7 можно сделать вывод, что процесс обжига во многом способствует повышению и однородности качества анодов.
Показания контроля качества в процессе производства подтверждаются исключительными показателями работы анодов на электролизерах. Графики на Рис. 8 показывают эволюцию ключевых показателей работы анодов в 2011 году.
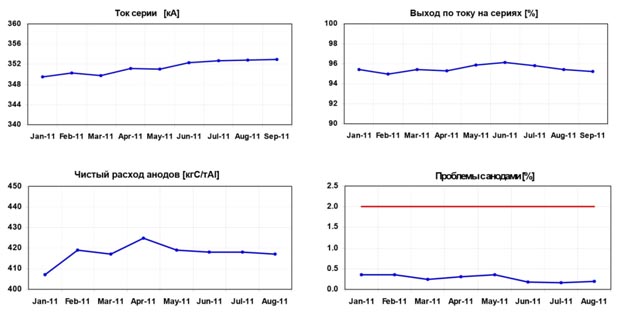
Управление сгоранием пека и потреблением энергии
Для полного сжигания пековых газов и полного использования тепла его сгорания для снижения до минимума общее потребление энергии первостепенное значение имеет эффективность поступления кислорода в зону дегазации. Потребление энергии также снижается при увеличении количества предварительно нагретого воздуха из камер охлаждения Печь обжига и система огня спроектированы и построены так, чтобы снизить до минимума сопротивление газовых потоков в огневых простенках и в вытяжном манифольде. Моделирование с помощью вычислительной гидродинамики стало инструментом первостепенной важности при проектировании печи обжига и всех компонентов системы огня.
Ранее сообщалось, что снижение до минимума потребления энергии не должно являться главной целью обжига [2], а, скорее, является результирующим моментом первостепенных целей обжига анодов, таких как качество анода.
С учетом характеристик сырья и зеленых анодов кривая обжига была адаптирована и оптимизирована до соответствующего уровня. Основной целью является обеспечить ровно необходимое количество энергии и предотвратить пережог анодов. Было проведено исследование влияния окончательной температуры обжига на потребление энергии [3]. При повышении температуры обжига на 50 °C (5%) потребление энергии увеличивается примерно на 10 % или приблизительно на 0.2 ГДж/т анодов.
Расчеты показали, что в результате вышеприведенных мероприятий удельное потребление природного газа составило 1.69 ГДж/т анодов на работающей на газе печи ABF 1 с циклом огня 29 часов и 1.55 ГДж/т анодов на печи ABF 2, работающей с циклом огня 27 часов.
Низкое потребление энергии, практически бездымное сгорание летучих углеродистых веществ (см. Рис. 9) и очень низкие показатели выбросов подтверждают высокий уровень общей эффективности сгорания.
Охлаждение анодов и потребление кокса для пересыпки
При высокой производительности кассет, составляющей 865 кг/час, эффективность охлаждения анодов с целью предотвращения выгорания на воздухе и безопасность выгрузки и обращение с анодами приобретает большое значение.
Недостаточное охлаждение анодов может быть результатом:
- Недостаточного количества охлаждающего воздуха
- Слишком крупного размера зерен материала пересыпки
- Избыточного давления охлаждающего воздуха
Избыточное давление охлаждающего воздуха и слишком крупный размер зерен материала пересыпки приводит к возгоранию материала пересыпки и самым драматическим последствиям:
- Увеличения потребления материала пересыпки с менее чем 10 кг/т анодов до более чем 30 кг/т анодов.
- Недостаточного охлаждения анодов или даже повторного нагрева анодов.
- Выгорания поверхности анодов на воздухе
Таким образом, эффективность охлаждения можно оптимизировать увеличением до максимума количества и давления охлаждающего воздуха без возгорания материала пересыпки, что выражается в оптимизации гранулометрии зерен.
Количество охлаждающего воздуха и, соответственно, энергии на охлаждение, можно рассчитать, определив поток воздуха на всех отверстиях камер охлаждения на основе измерений температуры, скорости и давления. Измерения, проведенные на EMAL, в процессе производства показали, что средняя энергия на охлаждение составляет 880 МДж/т анодов. Данный уровень является очень высоким - типовая величина энергии на охлаждение на аналогичных печах обжига составляет от 700 до 850 МДж/т анодов.
Оптимальная гранулометрия материала пересыпки обеспечивается минимальным потоком воздуха сквозь материал пересыпки. Испытания, проведенные R&D Carbon, показали, что данное требование выполняется при материале размером менее 2 мм. Соответственно, не допускается добавление прямо в печь необработанного, непросеянного кокса. Крупный кокс допускается добавлять только при контролируемых условиях с однородным перемешиванием существующих материалов пересыпки.
На Рис. 10 показана значимость предупреждения возгорания кокса пересыпки. Теплотворная способность нефтяного кокса составляет 30 МДж/кг. При превышении потребления кокса пересыпки уровня 30 кг/т анодов, энергия сгорания полностью уничтожает эффект охлаждения.
Выполняя все вышеуказанные параметры и с помощью оптимизации всех параметров процесса охлаждения EMAL обеспечил потребление нефтяного кокса на уровне 9 кг/т анодов.
Выводы
Сотрудничество EMAL с высокопрофессиональными партнерами позволило достичь на печах обжига выдающихся показателей:
- 450000 тонн анодов производится в год на крупнейшей вновь построенной печи обжига, объединившей в себе хорошо зарекомендовавшие себя технологии и оптимизированные ключевые конструктивные особенности печей обжига и систем огня.
- Отличное однородное качество анодов контролируется лабораторией и подтверждено эксплуатацией в корпусах электролиза с отличными показателями работы электролизеров.
- Высокое качество анодов с минимальными отклонениями, высокая производительность кассет - 865 кг/ч и потребление энергии, сниженное до 1.55 ГДж/т, устанавливает новые ориентиры.
Эти показатели стали результатом глубоких исследований и разработки новых конструкций при тесном сотрудничестве с нашими партнерами.
ЛИТЕРАТУРА
[1] Markus Meier, “Influence of Anode Baking Process on Smelter Performance”, Aluminium 1-2 2010
[2] Felix Keller, Peter Sulger, Markus Meier, Dagoberto Severo, Vanderlei Gusberti, “Specific Energy Consumption in Anode Bake Furnaces”, Light Metals 2010, 1005 - 1010
[3] Dagoberto Severo, Peter Sulger, Felix Keller, Markus Meier, “Recent Developments in Anode Baking Furnace Design”, Light Metals 2011, 853 – 858
[4] Felix Keller and Peter Sulger, Anode Baking, Sierre, Switzerland, R&D Carbon Ltd. 2008
[5] Werner Fischer, Raymond Perruchoud, Markus Meier et al, Anodes for the Aluminium Industry, Sierre, Switzerland, R&D Carbon Ltd. 1995
[6] Werner Fischer, Raymond Perruchoud, Markus Meier et al, Anodes for the Aluminium Industry 1995 - 2005, Sierre, Switzerland, R&D Carbon Ltd. 2005